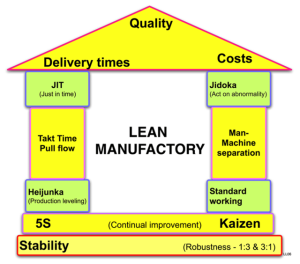
Abstract:
In the 1990’s a new term “Lean Manufacturing” was dubbed to replace the negative connotations of TPS. In a nutshell, Lean is a philosophical and methodological approach that strives to provide ever-increasing value to the customer through total employee involvement in the reduction of non-value-added activities and their associated costs. The main challenges which the garment industry is facing are labor cost for production processes, small quantities with few repetitions, frequently changing styles and short delivery times. These problems were addressed in this work by the implementation of lean tools like cellular manufacturing, Value stream mapping, single piece flow, work standardization, 5S etc. Lean manufacturing is an integrative concept use for identification and elimination of wastes related to production. The main purpose of implementing lean tool is to increase productivity, reduce lead time, improve poor line balancing, reduce WIP, improve quality, increase flexibility in design, reducing cost, etc. Under the highly competitive pressure the garment industry has a good scope for improvement using lean principles. Lean concept must be implemented in the fashion industry as companies always need to be prepared to respond to unexpected changes.
Keywords: TPS, Lean tool, fashion industry, Lean manufacturing etc.
Article:
Introduction
The lean manufacturing or lean production uses lean word as it uses less of everything in comparison to mass Production. Lean describe a system that produces what the customer wants and when they want it, with minimum waste – it is based on the Toyota production system. The concept of lean arises when company want to make the process more efficient, without delays and with less capital. The term lean implies the identification and elimination of waste in all the process involved in manufacturing. Lean manufacturing can be applied to any process and it brings a great result for sure. Lean manufacturing is a management philosophy that focuses on continuously improving all the processes involved in a manufacturing firm, irrespective of what type of product are being produced. Lean manufacture has a comprehensive set of rule, elements and tools which focus on the elimination of waste and the creation of value. The aim of this article is to understand the lean process in the perspective of apparel manufacturing that is beneficial to the industry itself and its purposes.
What is TPS?
The Toyota Production System (TPS) is an integrated socio-technical system, developed by Toyota, that comprises its management philosophy and practices. The TPS organizes manufacturing and logistics for the automobile manufacturer, including interaction with suppliers and customers. The system is a major precursor of the more generic “lean manufacturing”. Taiichi Ohno and Eiji Toyoda, Japanese industrial engineers, developed the system between 1948 and 1975.[1] Originally it was called “just-in-time production“. The approach created by the founder of Toyota, Sakichi Toyoda, his son Kiichiro Toyoda, and the engineer Taiichi Ohno. The principles underlying the TPS are embodied in The Toyota Way or TPS.
Wastage:
There are different type of wastage in apparel manufacturing. Sometimes, a product is manufactured more than the demands of a customer. And for material, information, equipment, tools, etc. Transportation is nothing but carrying of work in process (WIP) for long distance, insufficient transport, moving material from one place to another place is known as the unnecessary transport. When working on a product more than the actual requirements happen, then it is termed as over processing.Excess Inventory includes excess raw material, work in process, finished goods, obsolescence, damaged goods, transportation and storage costs.Defects in the processed parts is known as waste while repairing of the defective parts. And producing defective parts or replacing the parts due to its poor quality etc. is the waste of effort and time.Sometimes excess motion happens. Unnecessary motion is caused by poor workflow, housekeeping, poor layout and inconsistent or undocumented work methods. Value stream mapping is also used to identify this type of waste. And underutilized People includes under-utilization of the mental, creative, and physical skills and abilities.
Lean tools for apparel manufacture:
There are some systematic method for organizing and standardizing the workplace that is called 5S. TPM is important for smooth running of a production facility and gives the best utilization of machines with least disruption of production.Cellular Manufacturing is an integral part of lean manufacturing systems that is based upon the principles of Group Technology. VSM is used to find waste in the value stream of a product. Once waste is identified, then it is easier to make plan to eliminate it. KAIZEN is a strategy where employees work together proactively to achieve regular, incremental improvements in the manufacturing process.The Pareto diagram is a graphical overview of the process problems, in ranking order from the most frequent, down to the least frequent, in descending order from left to right. POKA YOKE is Design error detection and prevention into production processes with the goal of achieving zero defects. This method makes sure that the operator does not make any mistake while in operation. Kanban is a Japanese word that means instruction card. A Kanban can be any visual indication used to order the requirement of part or component. It is a manual pull device that allows an efficient means to transfer part from one shop to other.SMED focuses on simplifying machine setups. Reduce setup or change over time to less than 10 minutes and it focuses on increase production flexibility.JIT is Pulling the parts through production based on customer demand instead of pushing parts through production based on projected demand. It involves having the right items with the right quality and quantity in the right place at the right time. Visual Inspection makes the state and condition of manufacturing processes easily accessible and very clear to everyone.[2]
Existing system in apparel manufacturing:
Shirt manufacturing process consists of a series of different steps. The pre-production process includes designing the garment, pattern design, production pattern making, marking.The present manufacturing system uses batch system which is also called progressive bundle system.These bundles of parts are moved sequentially from one operation to other and gradually assembly process takes place through successive sub-assembly and main assembly operation in bundle form. In this system the sewing operations are aligned in a one continuous single line following the sequence of operation sequence order.Once the operation at one work station completed the WIP is pushed to next work station manually or by using trolley.After final sewing operation the work piece is send to quality checking point before sending in assembly section.[2]
Defining problem and objectives:
In garment industry it’s high time to adopt cellular manufacturing (Unit Production system), instead of existing Progressive bundle system (PBS) so that company will possess minimum WIP, as high WIP results in increasing the throughput time and as well as the flexibility of manufacturing firm can also be increased in order to meet customer changing need and demand. The main objective of implementing this tool is to minimize the work in process inventory and rework. Flexibility will be improved and it is the current demand of garment industry due to frequent change in fashion style. Labor cost will be reduced as less number of operations and operators will be required for doing the same amount of work.
Conclusions:
Lean manufacturing is a term that previously named as TPS as it was introduced for car production lines. But later Apparel manufacturers wanted to use it to reduce wastage and to adopt cellular production. This will reduce WIP, rework etc. And non-value adding operations would be reduced.
References:
-
Strategos-International. Toyota Production System and Lean Manufacturing.
-
Kumari, Rashmi. Quazi.T.Z., Kumar,Rishi. (2015). “Application of Lean Manufacturing Tools in Garment Industry”. IJMEIT Volume 3 Issue 1 Page 976