Abstract
The uncertain nature of the customer demand needs to be taken into consideration by generating the production plan and in particular the production quantities, to meet uncertain customer demand in the best way possible and maximize the profit, by minimizing production costs. Aggregate planning is a process by which a company decides about its ideal levels of capacity, production, inventory, stock-out situations, pricing, subcontracting, etc. Production planning is the correct placement of production orders concerning the place, or region, of production, and time scheduling and sequencing of production orders. The parameters are usually production rate, workforce, overtime, machine capacity level, subcontracting, backlog, and inventory on hand. The amount of overtime production planned is a parameter for aggregate production planning. Production planning for fashion apparel products has to cope with demand uncertainties. Collaborative forecasts created by various enterprises are an important input in aggregate supply chain planning. However, at the time of generating the production plan, the predicted customer demands are largely uncertain.
Keywords: Supply chain planning.
Article:
Introduction:
Supply Chain Planning (SCP) is a strategy for maintaining trade-offs between the supply of and the demand for goods and services. SCP is one of the primary elements of supply chain management, while the other is supply chain execution. The aggregate planning methods are used to decide about production, outsourcing, and backlogs in a supply chain.
A company’s supply chain
Supply chain planning covers many aspects of a company’s overall supply chain. Use of tools or inventory, sales, or production is included in SCP. Precise planning helps just-in-time inventory management requirements easier. A multi-screen dashboard can make the business process transparent using specific interface strategies. These things help supply chain managers save money and allow them to work efficiently.
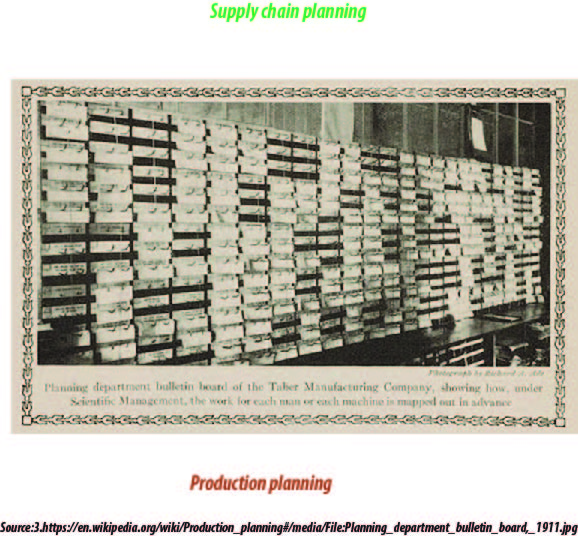
Aggregate planning
Aggregate planning is a process by which a company decides about its ideal levels of capacity, production, inventory, stock-out situations, pricing, subcontracting, etc. over a specified time. The goal of aggregate planning is to satisfy demand and maximize profit. It does not center aggregate planning around stock-keeping unit-related decisions only but solves aggregate decision problems. To be effective, it needs planning from around the supply chain and its results have an enormous effect on the whole supply chain performance. Collaborative forecasts created by various enterprises are an important input in aggregate supply chain planning. Many constraints in supply chain planning are because of other partners outside the enterprise.
Objectives of the aggregate planner
The aggregate planner’s primary aim is to identify some parameters in a specified time. The parameters are usually production rate, workforce, overtime, machine capacity level, subcontracting, backlog, and inventory on hand. Production rate is nothing but the number of units to be completed per unit time. The number of workers or units of capacity needed for production is also a parameter named the workforce. The amount of overtime production planned is a parameter for aggregate production planning. The number of units of machine capacity required for production (machine capacity level). The subcontracted capacity is needed over the specified time horizon (subcontracting). Demand not specified in the time and deferred for a future period is called backlog parameter. Inventory on hand is a parameter that denotes inventory carried over in a time.
Production planning process
Production planning helps businesses run more efficiently by optimizing product design and production. Originally used in manufacturing, it is currently used in the design, development, and delivery of software. In order to more successfully and efficiently achieve customer expectations, the production planning process entails forecasting product demand, weighing production possibilities, selecting the most efficient option, tracking and assessing progress, and modifying plans as necessary. To guarantee optimal execution, this procedure include assessing potential modifications, accounting for available resources, and researching both recent and historical market trends.
Production planning in the apparel supply chain
The uncertain nature of the customer demand has to be taken into consideration by generating the production plan and in particular the production quantities, to meet uncertain customer demand in the best way possible and maximize the profit, by minimizing production costs. Production planning is the correct placement of production orders concerning the place, or region, of production, as well as time scheduling and sequencing of production orders. It is of high economic importance for fashion apparel suppliers. However, at the time of generating the production plan, the predicted customer demands are uncertain. It is crucial to produce a robust production plan, which can manage the risk resulting from the demand forecast. Production planning for fashion apparel products has to cope with demand uncertainties. [1]
Conclusion
If demand and production capacity suggest an enterprise could make and sell 10,000 units but she can only afford supplies for 8,000 units, they require it to use the lower figure of her supplies. The forecast tells how much they need to produce to meet demand so that the enterprise knows the number of supplies they will need to maintain productivity. Previous experience can be used as a guide, and industry trends, economic forecasts, and feedback from their marketing/sales manager to determine the probable demand for their products in the coming months. The enterprise needs to anticipate the demand for their products before they can plan their supply ordering. They can evaluate their production department to determine how many products can reasonably produce during the period they are planning for. If they plan to borrow to buy supplies, include the interest costs in your estimates of the profits they will make from the products they manufacture. In other words, what they need to produce must always be compared to what you can afford to produce.
References
1. Ait-Alla. Abderrahim, Teucke. Michael, Lütjen. Michael, Samaneh Beheshti-Kashi. Samaneh, and Karimi. Hamid Reza. (2014). “Robust Production Planning in Fashion Apparel Industry under Demand Uncertainty via Conditional Value at Risk”. Mathematical Problems in Engineering.Volume 2014, Article ID 901861, 10 pages.http://dx.doi.org/10.1155/2014/901861
2. Johnston, Kevin. “Aggregate Planning in Supply Chain Management”.https://smallbusiness.Chron.com/aggregate-planning-supply-chain-management-73641.html
4, https://youtu.be/H05w66JKQ-c?si=8LzZeyRBYsISO0yg
5, https://rumble.com/v3k1d5g-how-supply-chain-planning-works.html